Growing pains for 3D printing
This article first appeared in the 2018 Physics World Focus on Optics and Photonics
Peter Leibinger, chief technology officer at the industrial laser and machine-tool firm TRUMPF, discusses progress in additive manufacturing and explains why the technology is currently going through puberty
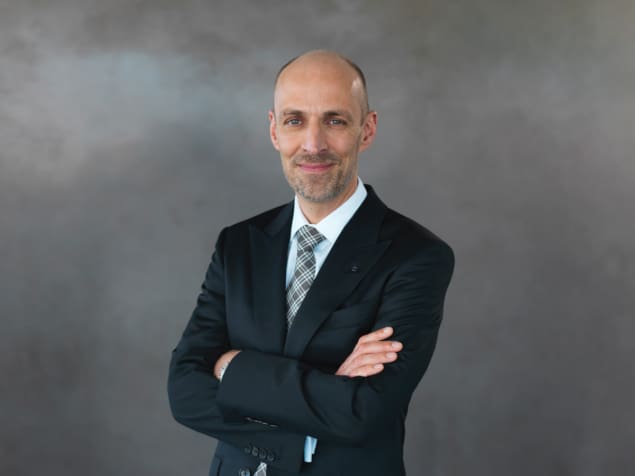
How did TRUMPF get involved in additive manufacturing?
We started working with additive manufacturing as early as the mid-1990s, when we experimented with using CO2 lasers for powder-type additive manufacturing. We then switched to solid-state lasers and developed a powder-bed additive manufacturing machine – where the laser creates new parts by building up layers from metal powder and fusing them together – that we introduced to the market in 2003. But unfortunately, the market was not ripe for it. People did not understand either the technology or the potential for it, and after three years without much success, we discontinued it.
In parallel, we continued offering powder-nozzle laser-based additive manufacturing, which is a different technique where the laser generates a weld pool on the component surface and powder is continuously added and melted onto it. But after a few years, we saw that the few customers we did have for our original powder-bed machine were really starting to understand its potential, and they began to approach us with requests to buy additional machines. That’s when we decided to restart this activity. Both types of manufacturing have their advantages and disadvantages. With the powder-bed design, for example, the surface quality and the overall part accuracy is much better, but the maximum part size is smaller and the productivity is lower because the process is slower by approximately a factor of five.
What did you learn from that first powder-bed machine?
We only sold 15 units over three years, and what was really discouraging was that the numbers were declining: the first year was the most successful year and it went down from there. We learned two things from that. One is that, obviously, you can be too early with the technology and the market. But we also learned that if you introduce a completely novel process for making parts, educating your users is important. We should have started by spending more effort on educating potential customers before trying to sell them a machine for $500,000 or $750,000.
What happened to make it possible to go ahead and produce those machines again?
A number of things. First is that advances in 3D computer-aided design systems gave people an ability to design intricate parts that simply wasn’t there before. Second, the experience with 3D printing plastic materials led people to understand that this technology has possibilities that can only be realized if you can do the same or similar processes in metal. And third, the powder-bed machines and processes became more productive and reliable than they were just after the turn of the millennium.
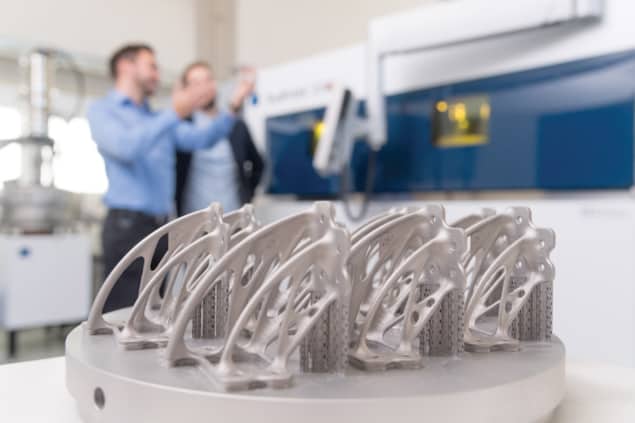
Now that the sector is over that initial hump, there’s a lot of hype about additive manufacturing. What are the benefits and drawbacks of that?
One benefit is that because there is a lot of attention being paid to the field, there are a lot of players willing to invest. Another is that for this technology to develop further, a collaborative effort is required – it’s not sufficient for machine builders or powder producers to just focus on what they do in isolation – and the hype helps this collaborative effort. Finally, there is a market there where there wasn’t one before, and that helps the producers and developers of new machines to survive because they can generate sales revenues.
The drawbacks of the hype are the expectations created within the customer base. I think that a lot of CEOs read articles in mainstream media about 3D printing and ask their CTO: “Why aren’t we doing anything?” They have an expectation that within one, two or three years, introducing additive manufacturing will bring about real benefits for the company’s bottom line, but in reality it probably won’t happen that fast. So there is a chance of disillusionment, and I’m concerned about that because it could throw a lot of good players out of the market because they wouldn’t survive a “valley of death” – but that is speculation.
How do you avoid that disillusionment? You talked about education.
At my own company, I spend a lot of time trying to manage expectations about how fast and how big our additive manufacturing business can grow. But yes, I do think it’s important to talk to customers and explain to them what they can expect and how much they need to invest in educating their own staff if they want to be able to reap the benefits. The field of additive manufacturing is growing up, but right now, it has essentially reached puberty. I mention this because I have four children and at least two of them are in puberty right now, so I can see that it’s a wonderful age – they get very enthusiastic very quickly. But they are also a bit too enthusiastic sometimes, and then they get very frustrated at other times.
There is a chance of disillusionment, and I’m concerned about that because it could throw a lot of good players out of the market
What’s your current wish list for improvements or innovations in this field?
I think the robustness of the additive manufacturing process must be improved, and that can be done through intelligent sensing and good use of the data generated through those sensors. If we can learn from things that we see happening in the process and adjust the machines accordingly, that would be very good because we have to be able to adapt to different powder qualities and climate conditions. At the moment, if the Sun shines in the afternoon, sometimes we get a different part quality than we did in the morning. I’m exaggerating a bit, but that’s what it’s like, and better sensing could help.
AdvertisementWhat about more fundamental advances, such as in materials science or laser optics?
Those are also important – for instance, it might be nice to expand the types of laser sources used, the available wavelengths and so on. However, we have to keep in mind that these processes take a long time. If we develop a new type of laser source for additive manufacturing, we’re talking five years from the beginning of the project until we see the first part being printed and in production, and that’s a long time. The most immediate problems to be solved are the robustness of the process. Once we have that, we can expand the field.
What developments do you expect to see in the next five years?
I expect to see a fragmentation of the market in terms of the processes used for individual parts. We will probably see more hybridization, where different types of additive manufacturing are used in combination with each other or with traditional subtractive techniques. There are a lot of new companies entering the field, and in the next few years we are going to see a learning process where the community will come to understand which technique is best for which type of part
No comments:
Post a Comment